Pandemic-proofing our future: 3D-printed face masks to prevent outbreaks
By Josh Piers - - 5 Mins Read
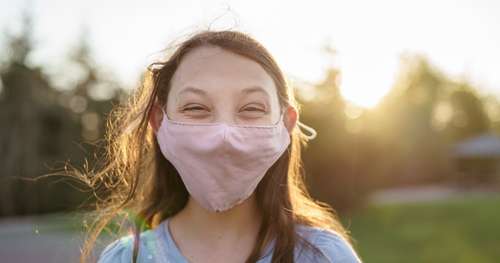
As the supply of personal protective equipment (PPE) diminished in the face of Covid-19's attack, photos of doctors and nurses wearing repurposed waste bags, swim goggles, and snorkeling masks became some of the most unforgettable images of the early pandemic.
Those photos demonstrated how unprepared we were to deal with a pandemic that spread quickly. PPE was primarily reliant on foreign suppliers in the United Governments, particularly in China, and there are no rules mandating hospitals or states to store a set level of stock in case of a crisis.
Most didn't because US health care is under a financial strain, and just-in-time sourcing is more cost-effective in normal circumstances. As a result, there was a supply shortage, which impeded our response to the pandemic.
As the country awaited US manufacturers to ramp up PPE production and supply chains to stabilize, 3D printing appeared as an intriguing bridging alternative.
Faced with a scarcity of masks, a coalition of private, public, and volunteer organizations banded together to fill the hole, focusing on the production and distribution of 3D-printed masks.
To be sure, their efforts were insufficient to cover the gap. But, as a stopgap, they clearly helped, particularly at the local level, where such activities were concentrated, all of which implies that 3D printing has a limited but promising role to play in the battle against future pandemics.
A frantic search for masks and other protective gear
It's difficult to overstate the severity of the PPE problem in the early days of the epidemic, especially for healthcare personnel on the front lines.
The scarcity prompted a scramble for masks and other supplies, pitting hospitals and states against one another. Hennepin Healthcare's medical director for emergency preparedness, John Hick, recounts the extent to which his hospital had to go to get shipments from the increasingly scarce supply. "We had a feeling the supply chain wouldn't be able to keep up with the pandemic and it didn't," he adds.
Meanwhile, Chinese supply businesses attempted to circumvent early-pandemic export limitations imposed by the Chinese government. "A lot of times when we were receiving samples of masks and gowns from China, they would come in a box covered with clothing," Hick explained, "so that from an export standpoint, it would look like they were delivering those and not PPE."
The promise of printing PPE in a pandemic crisis
Digital drawings may be turned into tangible, three-dimensional items with 3D printers. Material such as polymers or metal powders are set down in successive layers, one added after another, following a digital plan – one reason 3D printing is also known as additive manufacturing.
3D printers can produce real products like face shields and masks in a matter of minutes or hours if they have enough raw material and a digital design to work with.
According to a study conducted by America Makes, the initiative resulted in the production and delivery of 38 million face shields and face shield parts, over 12 million Covid-19 diagnostic nose swabs, over 2 million ear savers, and hundreds of thousands of mask components and ventilator parts.
It's far from flawless. Additive manufacturing is typically used for developing designs rather than full-scale production but the urgent demand for PPE early in the pandemic allowed an opportunity to test the technology's boundaries.
It's a band-aid, not a long-term solution.
3D printing is fundamentally small-scale, as those data imply. It's not a long-term solution for addressing the healthcare system's PPE need, and it'll never be as cost-effective as traditional mass manufacturing at scale. Its primary benefit is that it can be done locally with little lead time, and it can temporarily bridge the gap while larger-scale manufacturing and shipping catch up.
However, additive manufacturing is just that. Reforming supply chains and increasing emergency stockpiles of traditionally manufactured PPE will be required to prepare for the next pandemic.
Moving away from just-in-time shipment for PPE, tax incentives or hospital rules to incentivize PPE manufacture year-round, and new mechanisms to improve visibility of PPE supply and chains between hospitals and states are just a few of the upgrades on the wish list.
However, we now have a better understanding of the limitations of 3D printing in an emergency and how far we can push them. This time, it almost probably saved some lives, and it could be even more important in the next pandemic.